PCB Process Capability
No. | Project | Technical indicators |
1 | Layer | 1-60(layer) |
2 | Maximum processing area | 545 x 622 mm |
3 | Minimumboardthickness | 4(layer)0.40mm |
6(layer) 0.60mm | ||
8(layer) 0.8mm | ||
10(layer)1.0mm | ||
4 | Minimum line width | 0.0762mm |
5 | Minimum spacing | 0.0762mm |
6 | Minimum mechanical aperture | 0.15mm |
7 | Hole wall copper thickness | 0.015mm |
8 | Metallized aperture tolerance | ±0.05mm |
9 | Non-metallized aperture tolerance | ±0.025mm |
10 | Hole tolerance | ±0.05mm |
11 | Dimensional tolerance | ±0.076mm |
12 | Minimum solder bridge | 0.08mm |
13 | Insulation resistance | 1E+12Ω(normal) |
14 | Plate thickness ratio | 1:10 |
15 | Thermal shock | 288 ℃(4 times in 10 seconds) |
16 | Distorted and bent | ≤0.7% |
17 | Anti-electricity strength | >1.3KV/mm |
18 | Anti-stripping strength | 1.4N/mm |
19 | Solder resist hardness | ≥6H |
20 | Flame retardancy | 94V-0 |
21 | Impedance control | ±5% |
We do Circuit Boards Prototyping with 15 years' experience with our professionalism
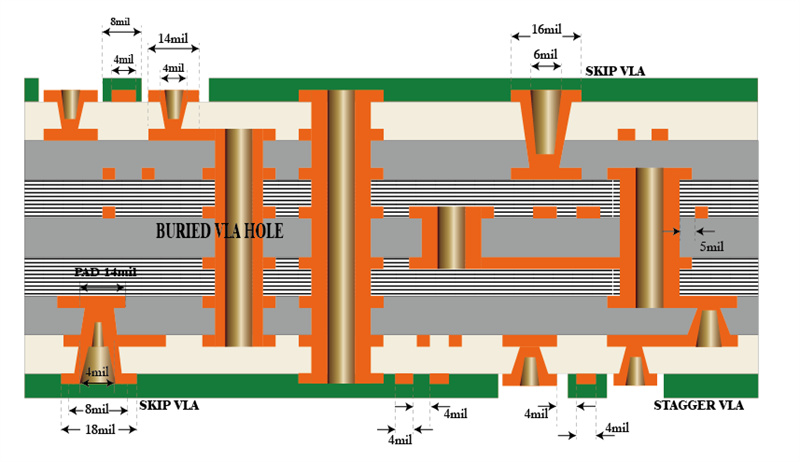
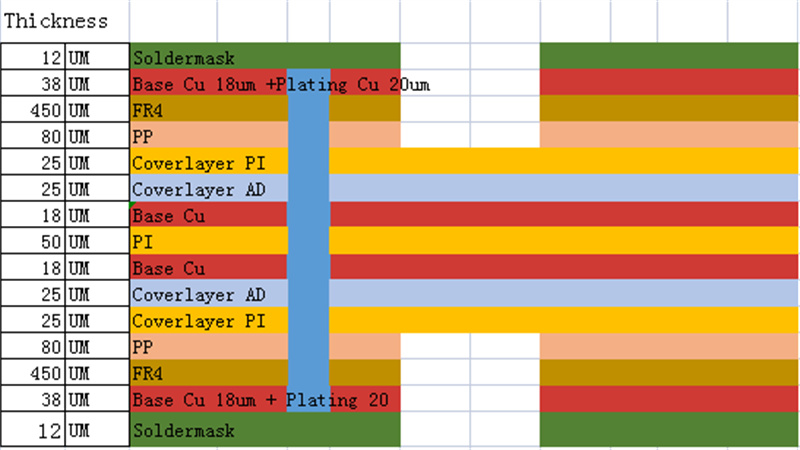
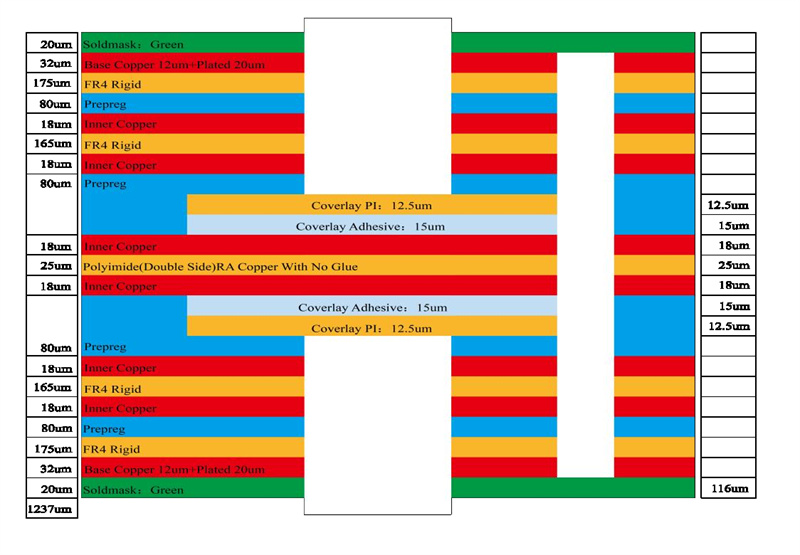
8 layer HDI Printed Circuit Boards
4 layer Flex-Rigid Boards
8 layer Rigid-Flex PCBs
Testing and Inspection Equipment
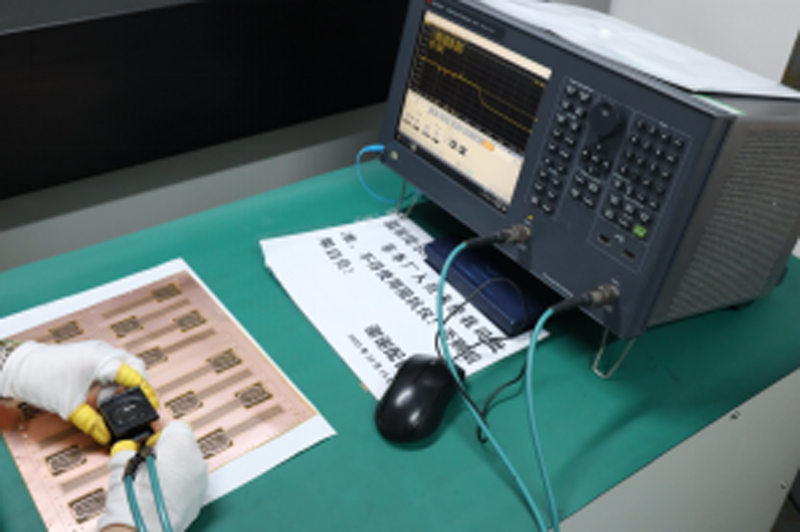
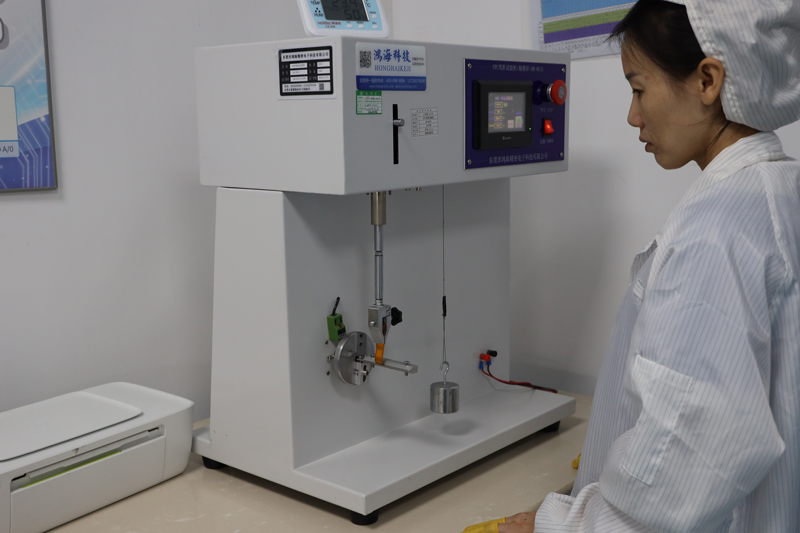
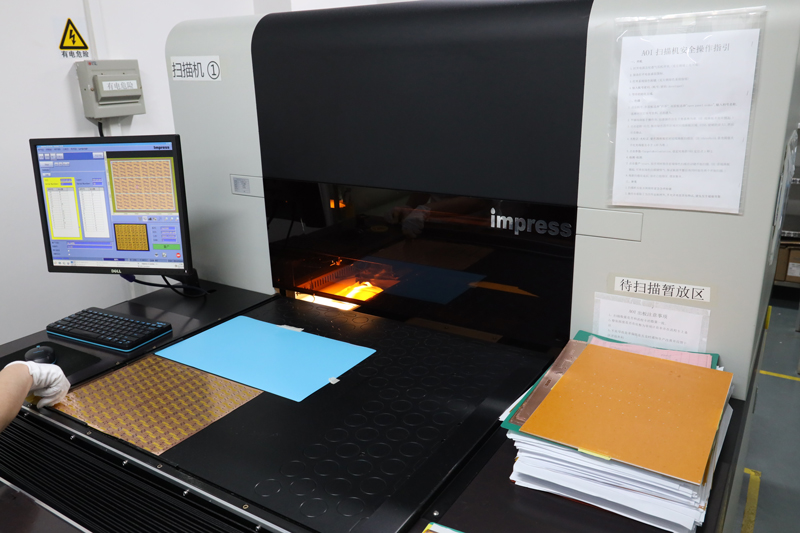
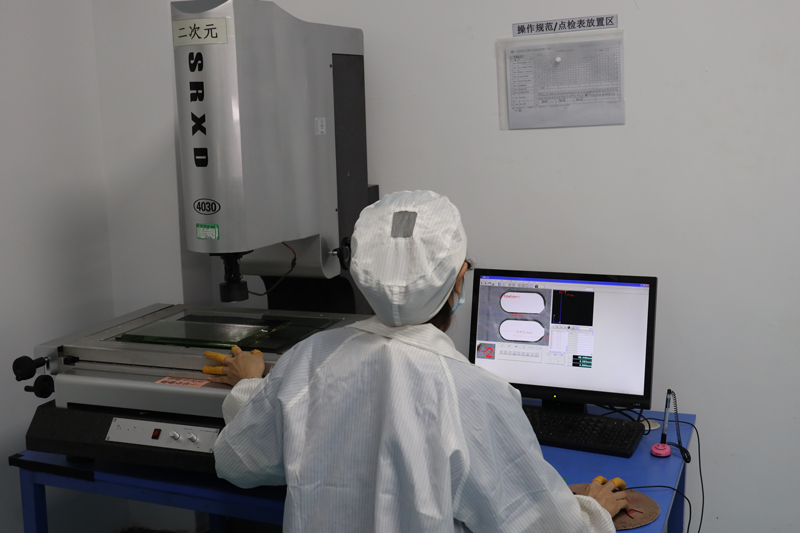
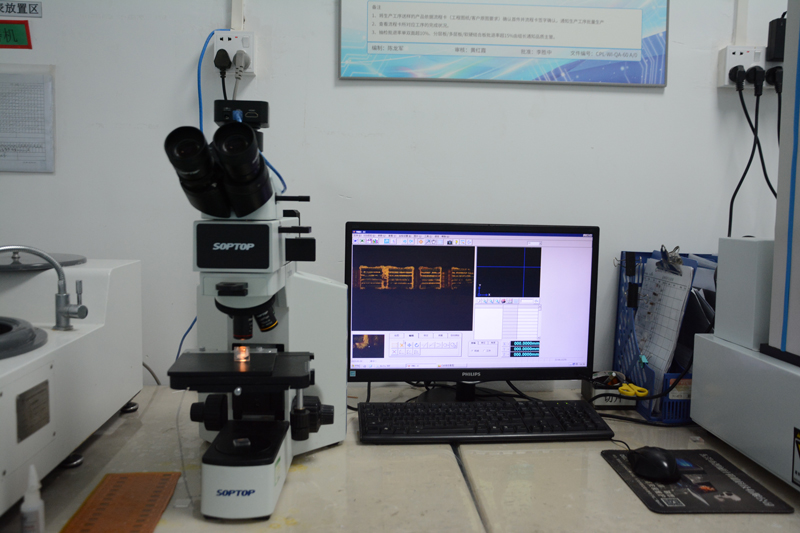
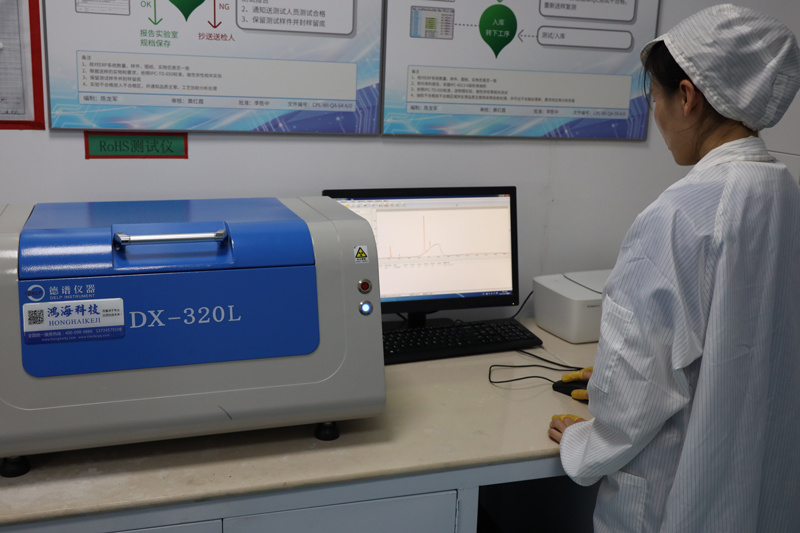
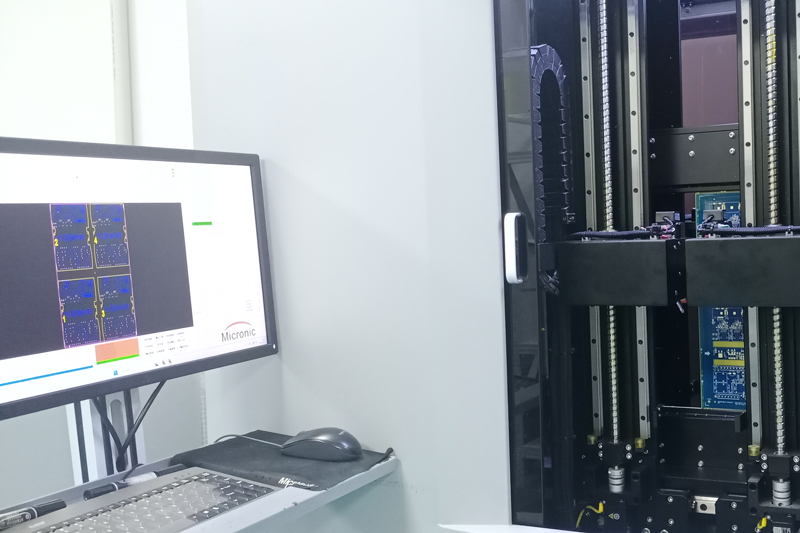
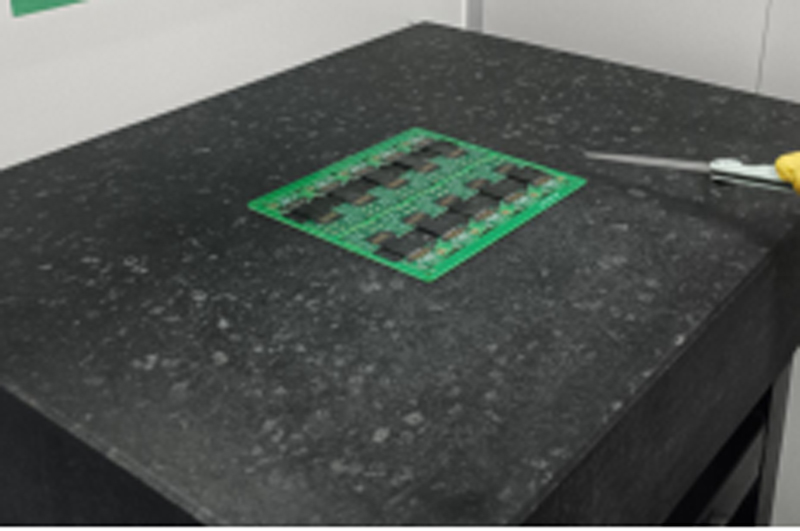
How to manufacture a high- quality Double-Sided Circuit Boards?
. Provide technical support Pre-sales and after-sales; . Custom up to 40 layers, 1-2days Quick turn reliable prototyping, Component procurement, SMT Assembly; . Caters to both Medical Device, Industrial Control, Automotive, Aviation, Consumer Electronics, IOT, UAV, Communications etc.. . Our teams of engineers and researchers are dedicated to fulfilling your requirements with precision and professionalism.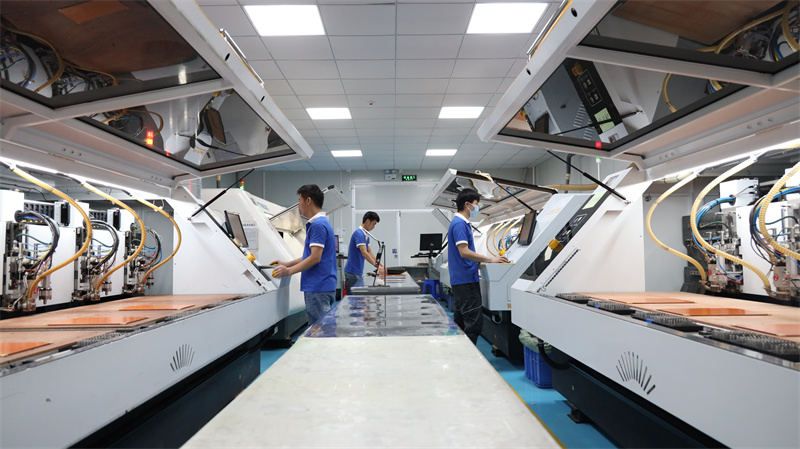
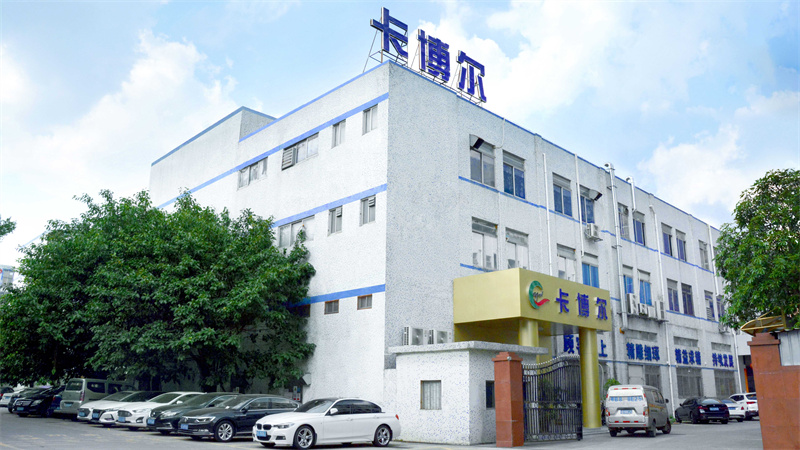
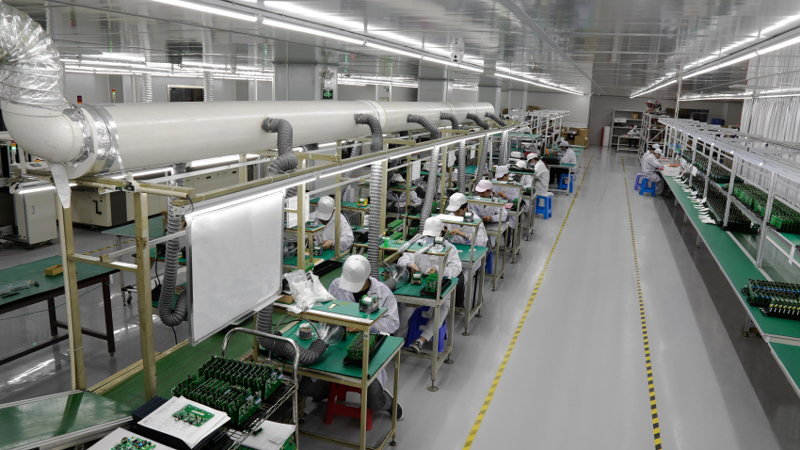
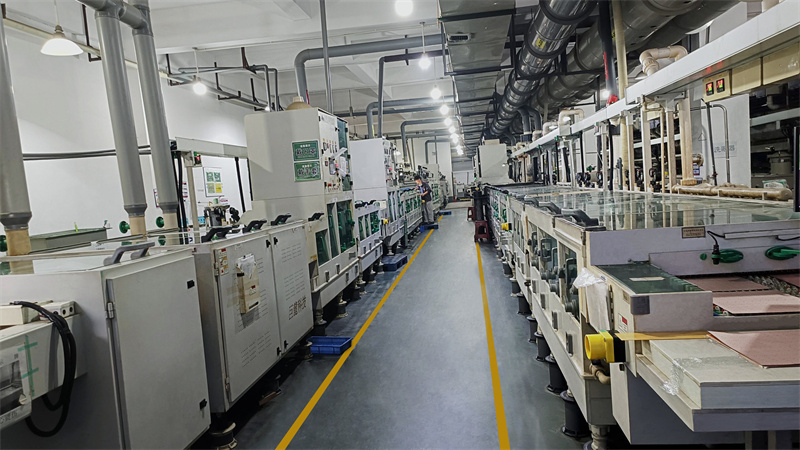
Our Circuit Boards Prototyping Service
1. Design the board: Use computer-aided design (CAD) software to create the board layout. Ensure that the design meets all electrical and mechanical requirements, including trace width, spacing, and component placement. Consider factors such as signal integrity, power distribution, and thermal management. 2. Prototyping and testing: Before mass production, it is critical to create a prototype board to validate the design and manufacturing process. Thoroughly test prototypes for functionality, electrical performance, and mechanical compatibility to identify any potential issues or improvements. 3. Material Selection: Choose a high-quality material that suits your specific board requirements. Common material choices include FR-4 or high-temperature FR-4 for the substrate, copper for conductive traces, and solder mask to protect components.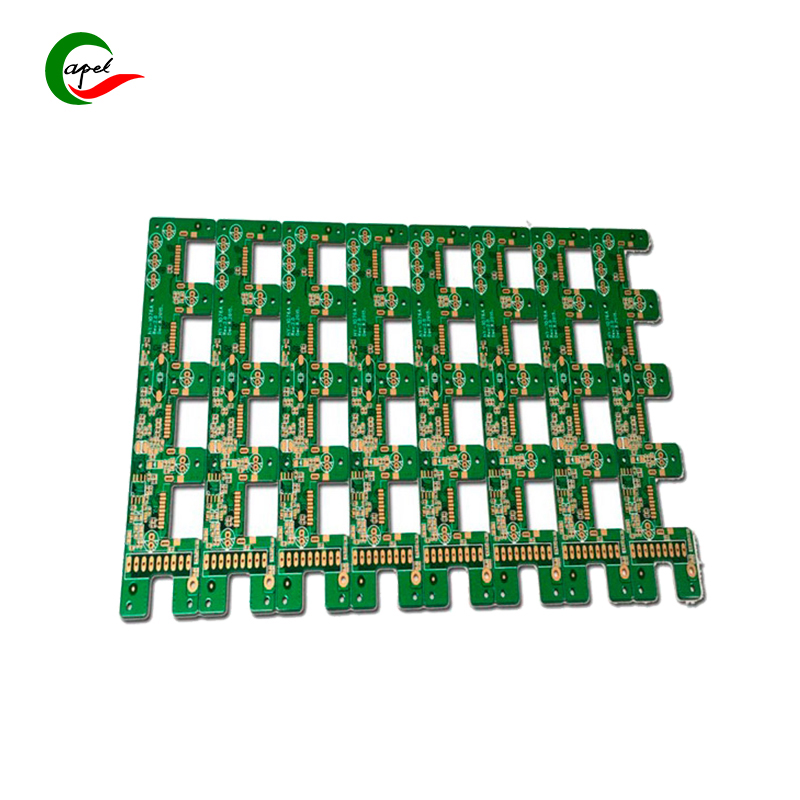
How to manufacture a high- quality Double-Sided Circuit Boards?
7. Electroless Copper Plating: Apply a thin layer of copper to all exposed interior surfaces. This step ensures proper conductivity and facilitates the plating process in subsequent steps. 8. Outer layer imaging: Similar to the inner layer process, a photosensitive dry film is coated on the outer copper layer. Expose it to UV light through the top photo tool and develop the film to reveal the circuit pattern. 9. Outer layer etching: Etch away the unnecessary copper on the outer layer, leaving the required traces and pads. Check the outer layer for any defects or deviations. 10. Solder Mask and Legend Printing: Apply solder mask material to protect copper traces and pads while leaving area for component mounting. Print legends and markers on top and bottom layers to indicate component location, polarity, and other information. 11. Surface Preparation: Surface preparation is applied to protect the exposed copper surface from oxidation and to provide a solderable surface. Options include hot air leveling (HASL), electroless nickel immersion gold (ENIG), or other advanced finishes.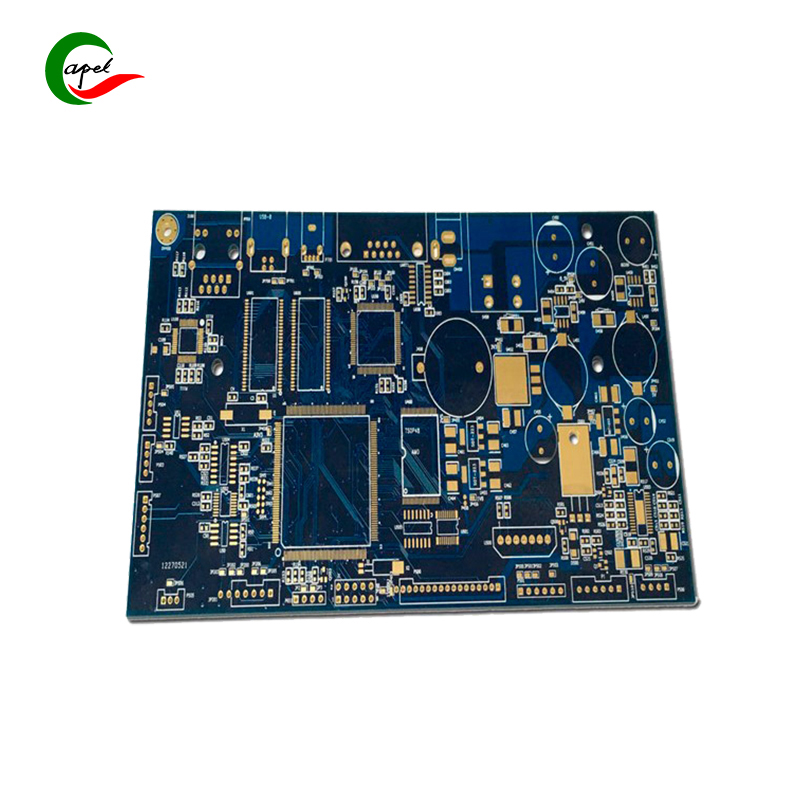